Mechanical assembly is the description of the connotation of putting component parts together to make a complete product or perform a function.
In the manufacturing and industrial context, mechanical assembly is the process used in assembly line production. As a product travels down the assembly line, a part is added at each work station. In some lines, the conveyor may stop at each station, while in other factory line set-ups, the conveyor may move continuously. As the part passes the work station, the worker or an industrial robot performs a task that contributes to the assembly of the completed product.
Mechanical assembly requires special engineering techniques to ensure cost-effective and on-time assembly of products. To design products for mechanical assembly, engineers must essentially build the product in the design and then disassemble it. By doing so, the engineer can decide the steps necessary to build the product in a logical order using assembly line technology.
This careful engineering is important because, if the steps are taken out of order, it could result in missing components. If this happens, the item would have to be disassembled to put parts in place. By creating a complete concept of the assembly process during the engineering phase, products can go into assembly line production in multiple plants using the plan and parts from a variety of sources. In many cases, parts not specifically engineered for a certain product, such as nuts and bolts, can be purchased from a low bidder, thus saving production costs.
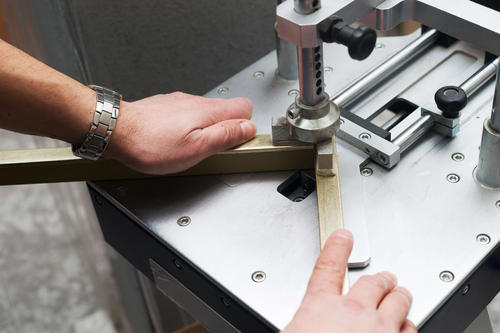
There are several advantages to using mechanical assembly as an industrial process. Products manufactured in this manner can be easily disassembled and reassembled in remote locations. Production costs are often lowered as component parts can be created off site and assembled in the factory. These products can also be repaired easily with in-stock replacement parts. With the ability to easily take apart mechanical assemblies and reassemble them, these products can be upgraded easily.