Plastics exusion is a continuous high-volume manufacturing process, in which raw plastic is melted and formed into a continuous profile. This process starts by feeding plastic material (pellets, granules, flakes or powders) from a hopper into the barrel of the extruder. The material is gradually melted.
Mechanical energy generated by turning screws and by heaters arranged along the barrel. The molten polymer is then forced into a die, which shapes the polymer into a shape that hardens during cooling.
Plastic extrusion can be done with a wide variety of materials:
Polyethylene (PE),
Polypropylene (PP),
Acetal,
Acrylic,
Nylon (polyamides),
Polystyrene (PS),
Polyvinyl chloride (PVC),
Acrylonitrile butadiene styrene (ABS).
Polycarbonate (PC).
Depending on the material used, the plastic product can be either rigid, semi-rigid or flexible, as well as have any number of interesting properties. At Keller, we can even manufacture your profile using specialty materials, such as biodegradable plastics or glow-in the-dark ones.
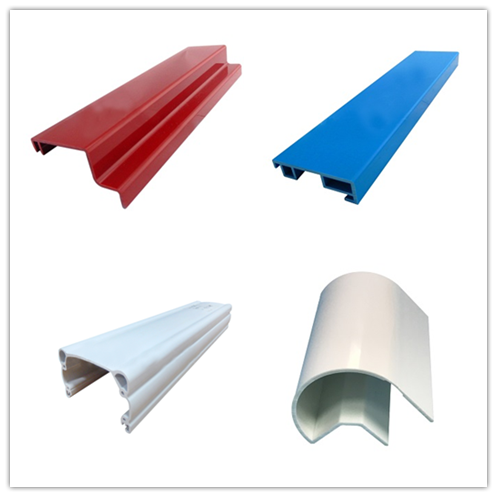
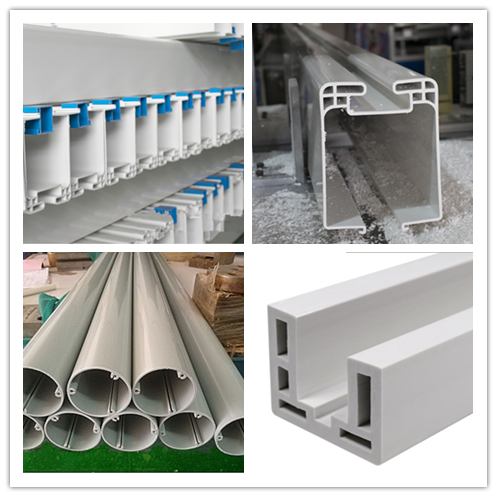